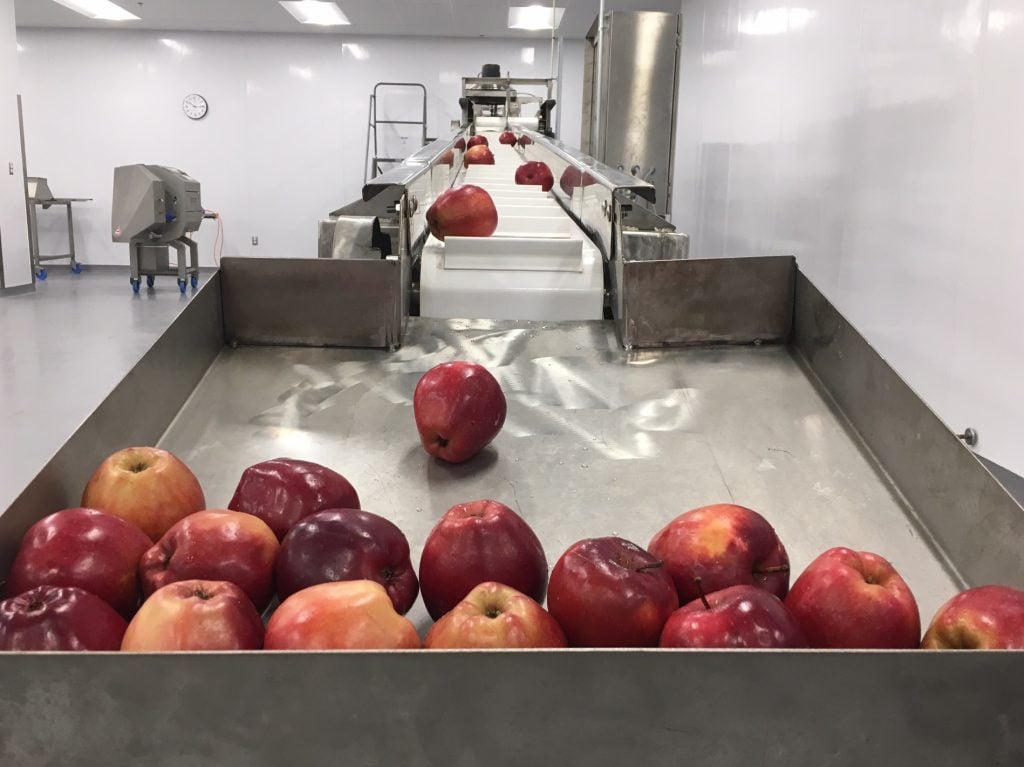
For the Foodlinkers hard at work inside our new Value-Added Processing Center, it seems they’ll now have to get a decent shoulder workout elsewhere.
Gone are the days of using a manual apple slicer, which required a forceful pull-down of a large, metal contraption that sliced two apples at at time, which barely yielded one case of apple slices per hour. Now, the automated line is up and running and Foodlink is slicing apples like never before.
It’s one component of the Community Kitchen that has transformed the way Foodlink serves the community.
“The joy of seeing kids eating apples that would normally be thrown away because they weren’t sliced is beyond amazing,” said Moses Ulom, Foodlink’s VAP Supervisor. “Hey, if the kids love it, then we love it too!”
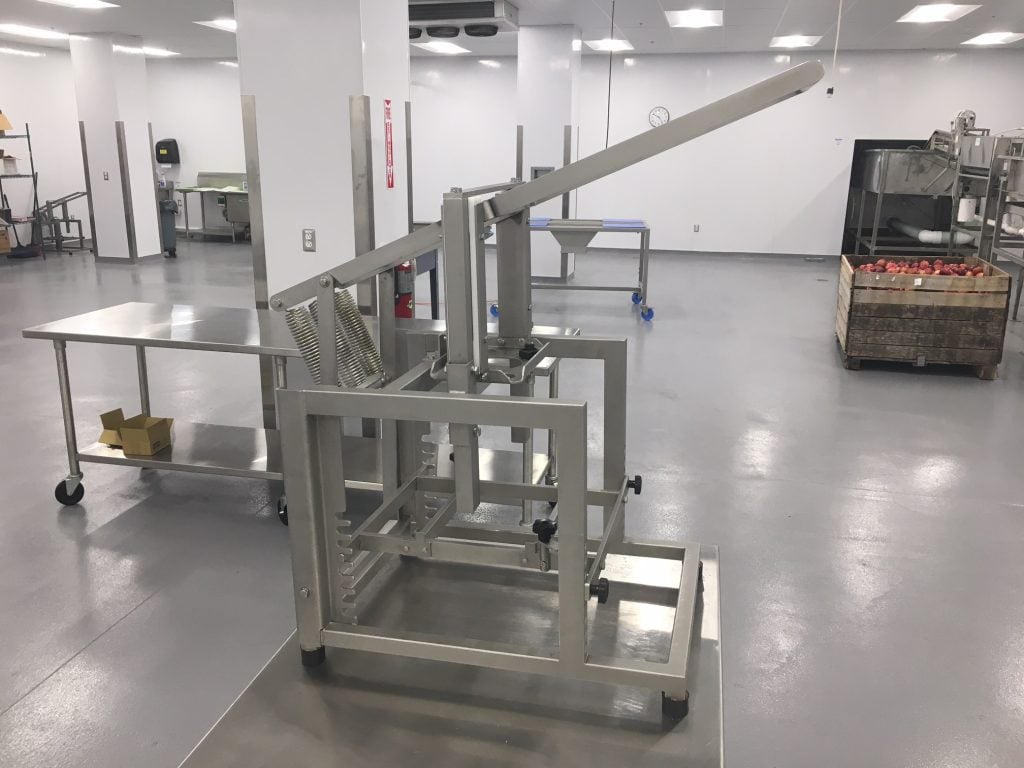
In 2012, Foodlink founder Tom Ferraro was approached with two apple-related issues. (1) There were kids in Wayne County schools that were eating Washington State apples. This made little sense, due to the fact that Wayne County is among the top apple-producing counties in the nation; and (2) A Cornell University study showed that children were much more likely to eat a sliced apple than a whole one if it was served to them at school. Simply put: Apple slices ended up in bellies. Whole apples ended up in trash cans.
Armed with this data, Ferraro agreed to take the idea and run with it. Foodlink’s apple-slicing operation, known as Value-Added Processing (VAP), began.
The program showed promising growth through the first few years. Last fiscal year, Foodlink sliced and distributed more than 50,000 pounds of apples. The slices are sold to two area distributors, which then provide them to local schools.
“After planning and talking about this apple line for a year and a half, it’s incredible to see it come to life,” said Terra Keller, Foodlink’s Chief Operating Officer. “It’s a key piece to our Community Kitchen, and one that will grow to meet the needs of our community. We look forward to collaborating with more distributors so we can send even more local apples into our local schools.”
With Foodlink’s new equipment up and running, expect numbers to increase as more partnerships are secured with distributors. Foodlink also intends to distribute sliced apples to its member agencies, as well as offer them to the Summer Meals and Curbside Market programs. As apples catch on, our VAP Center also intends to process other produce options, such as diced butternut squash, and carrot and cucumber coins.
In the first couple days of production, Foodlink’s VAP center produced 43 cases in roughly 8 hours of work. With the old method, that would have taken 43 hours — not to mention some sore shoulders.
“We started slicing apples using the hand corer, which wasn’t designed for mass production,” Ulom said. “It got even tougher as the demand for sliced apples began to increase daily. We explored many options, but none of them were efficient enough to help us accomplish our objectives. Thanks to our generous donors, Foodlink is now able to provide kids with more nutritious and delicious snacks to keep them healthy.”
The apple line is fairly complex, and incredibly long. From the apple bin to the bagger, it measures 86 feet with a few twists and turns along the way. From start to finish, here are the 10 main steps:
1) Washed
2) Dried
3) Sliced
4) Soaked
5) Sorted
6) Inspected
7) Bagged
8) Counted
9) Boxed
10) Shipped
It’s an amazing addition to Foodlink’s Community Kitchen, and certainly a dream come true for Moses and his colleagues. Getting more nutritious snacks in front of kids is essential to building a healthy, hunger-free community.
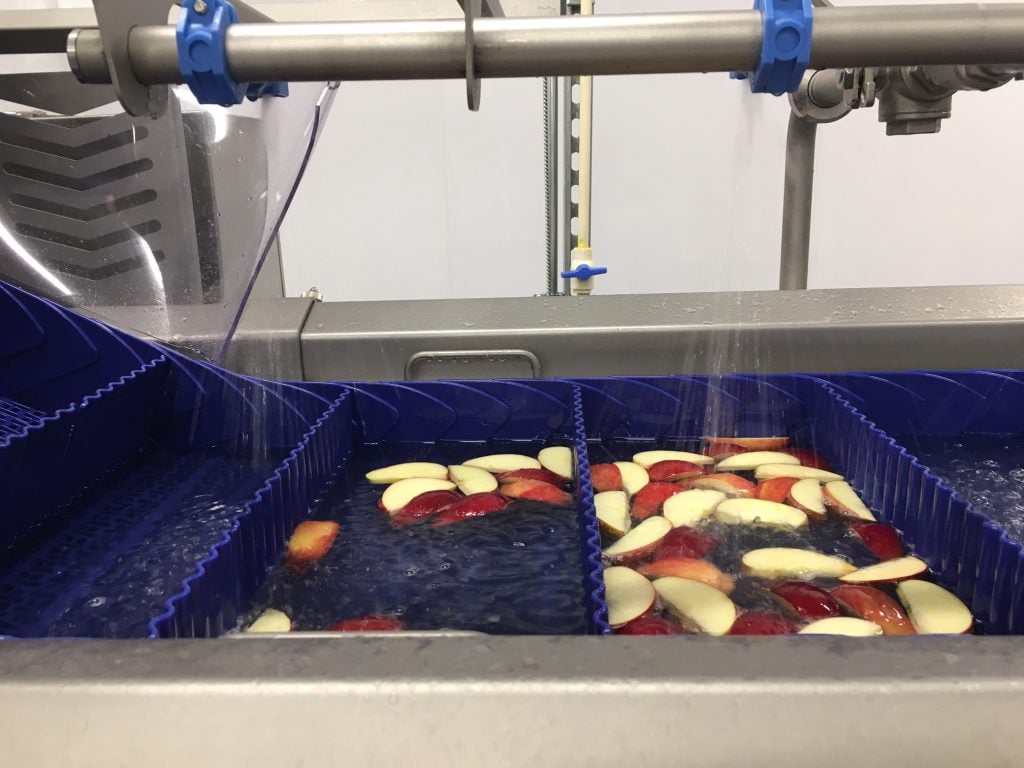